Super9 Infotech
Call us for demo : India - O79-29097621
079-40039117
USA - 1-732-203-7637
ERP - For Multiple Locations, Manufacturing, Engineering, Chemical, FMCG, Paints, Pharmaceutical, Distribution , Multiple Branches, Warehouse - Please call +91-9427616044 for your Resource Planning Needs.

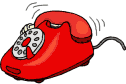
SUPER9 ERP Modules:
Sales Module:
​Roboustic Process while entering sales Order , so there is no need to write on the paper any more just enter in the system with only few keys. Value, Excise, Discount , Rebate , Vat and any other taxes will be derived automatically from master so entering person do not have to worry for all this while entering order. Price , Rebate and Discount can be setup on Item Basis as well as from Party wise.
User can select multiple orders against single dispatch number with one selection key and process the orders. If system does not have enough stock for specific item it will give user Red Alert . Users can change the dispatch quantity based on the available physical stock. System Use this control without hurting the speed of the sales dispatch process. One User can process min. 150 orders within 6 hours with all above mentioned controls.
ERP - For Multiple Locations, Manufacturing, Engineering, Chemical, FMCG, Paints, Pharmaceutical, Distribution , Multiple Branches, Warehouse - Please call +91-9427616044 for your Resource Planning Needs.

Reports​
Masters​​
- Sales Setup Options
- Route Code Master
- Vehicle Master
- Sales Discount Code Master
- Sales Price (Multiple) Master
- Sales Rebate Master
- Customer, Transporter Master
Transactions​
- Sales Order
- Sales Dispatch
- Sales Invoice
- Direct Sales Invoice
- Sales Summary
- Sales Dispatch Summary
- Route Sales Order Summary
- Sales Invoice Import
- Invoice Report
- Performance Invoice
- Sales Bill Outstanding
- Sales Invoice
- Outstanding Letter
- Form 402 Report
- Sales Register
- Vehicle Report
Purchase Module​:
Purchase Order : Roboustic Process while entering Orders. It would allow to enter line items with Barrel or Bucket or Kg or any other gross units. Value, Excise, Discount , Rebate , Vat and any other. Taxes will be derived automatically from master so entering person do not have to worry for all this while entering order. Item Previous Buyout price will automatically derived so person know the last buyout price of the specific material.
Purchase Receipt : Multiple Orders Receipts can be handled. Receiving Quantity person only can access the rights of Quantity Inwards so he/she does not View Value of the Purchase Order. Quantity can be received more or less than purchase order and system will track this. Goods Received Note will be printed out from the system. Also Quality Test can be handled at this level and if goods are not up-to the mark system record this and at the time of payment right
decision can be taken.
Purchase Invoice : System will allow direct as well as indirect purchase invoice System. Here user would know the Order qty, received qty and invoiced qty and based on that he would make an decision of payment of the specific invoice and therefore company can prevent any payment where Quantity is less inward or not up-to the Quality.• Also this Purchase Invoice handle cost which is not associated in the bill like Freight which we pay to transporter for the goods inward and which company has to bear – This will help system to add per unit cost (freight which is not part of the bill)
ERP - For Multiple Locations, Manufacturing, Engineering, Chemical, FMCG, Paints, Pharmaceutical, Distribution , Multiple Branches, Warehouse - Please call +91-9427616044 for your Resource Planning Needs.
Masters​​
- Purchase Setup Options
- Vendor/Supplier Master
- Document Attached Master
Transactions​
- Purchase Order
- Purchase Receipt/Inward
- Purchase Invoice
- Direct Purchase Invoice
- Purchase Summary
- Purchase Receipt/Inward Summary
- Purchase Return
- Miscellaneous Purchase/ Expense Entry


Reports​
- Purchase Register
- Purchase Bill Outstanding
- Purchase Invoice
- Purchase Slip
- Outstanding-Purchase Letter
- Raw Material Requirement Planning and Evaluation.
Production Module​​ ( Bill of Material):
BATCH ENTRY :
Master Batch will be created – This will plug raw material per unit cost into Semi-finished Batch. This will handle Weight per liter, Expiry date , Quality Parameters ,machine time, Person In-charge etc., Here System will change the batch Standard Quantity and the whole batch raw material or other semi-finished items configuration changes. If stock is not for any raw material it will give alert here. Batch card will be generated from this system.
BOM ISSUE :
Here user can issue the raw material to the floor by step wise or item wise and Raw material or Semi-finish stock will be reduce and Work in Process (Semi- finish) Stock will increase. Client will control complete stock of Raw material as well as how much value of the stock is on the floor as well as in the Store.
BOM PRODUCTION :
Packed Finished goods (like 20kg or 5kg ) entry will be made here by batch wise and it will track batch wise production i.e. client can analyze Yield, scrape and quality of the batch. If Batch Std Qty = 1000 kg for example. & Weight per liter = 0.90 , Expected Production = 1111.11 kg. - Tolerance limit = 3% (Allowed up-to1144.44 kg -- If user enter more than this system will not allowed user to enter and in this case batch manager/admin has to adjust wt/liter or tolerance or analyze the batch.
ERP - For Multiple Locations, Manufacturing, Engineering, Chemical, FMCG, Paints, Pharmaceutical, Distribution , Multiple Branches, Warehouse - Please call +91-9427616044 for your Resource Planning Needs.
Masters​​
- Bill of Material Master
- Packing Master
- Inventory Master
- Product line Masters
Transactions​
-
Batch Entry and Batch Transfer Entry
-
Batch Issue- Multiple Batch issue under one number.
-
Batch Production – Multiple FG production under one number with different batch.
Bank Module:
User can easily enter Bank or Cash Receipt / Payment and apply against outstanding invoice or against debit memo or credit memo and if any balance left it will go to on account section which will pop up every time user does any transaction for specific client. System generates daily basis vouchers and register for the Bank / Cash transactions. System generate sms (messages) to the customer about receipt as well as sales dispatch.
Masters​​
-
Bank Maintenance
-
Main Account Maintenance
Transactions​
- Advance Check Entry
- Bank/Cash Receipt
- Bank/Cash Payment
- Edit Receipt/Payment
- Reconcile Bank & Bank Transfer


Reports​
-
Batch Register
-
Issue Register by Serial number
-
Issue Register Batch Raw Material
-
Issue Register Production
-
Batch Details
-
Batch Register Production
-
Batch Analysis & Batch wise Production Report
-
Production Register
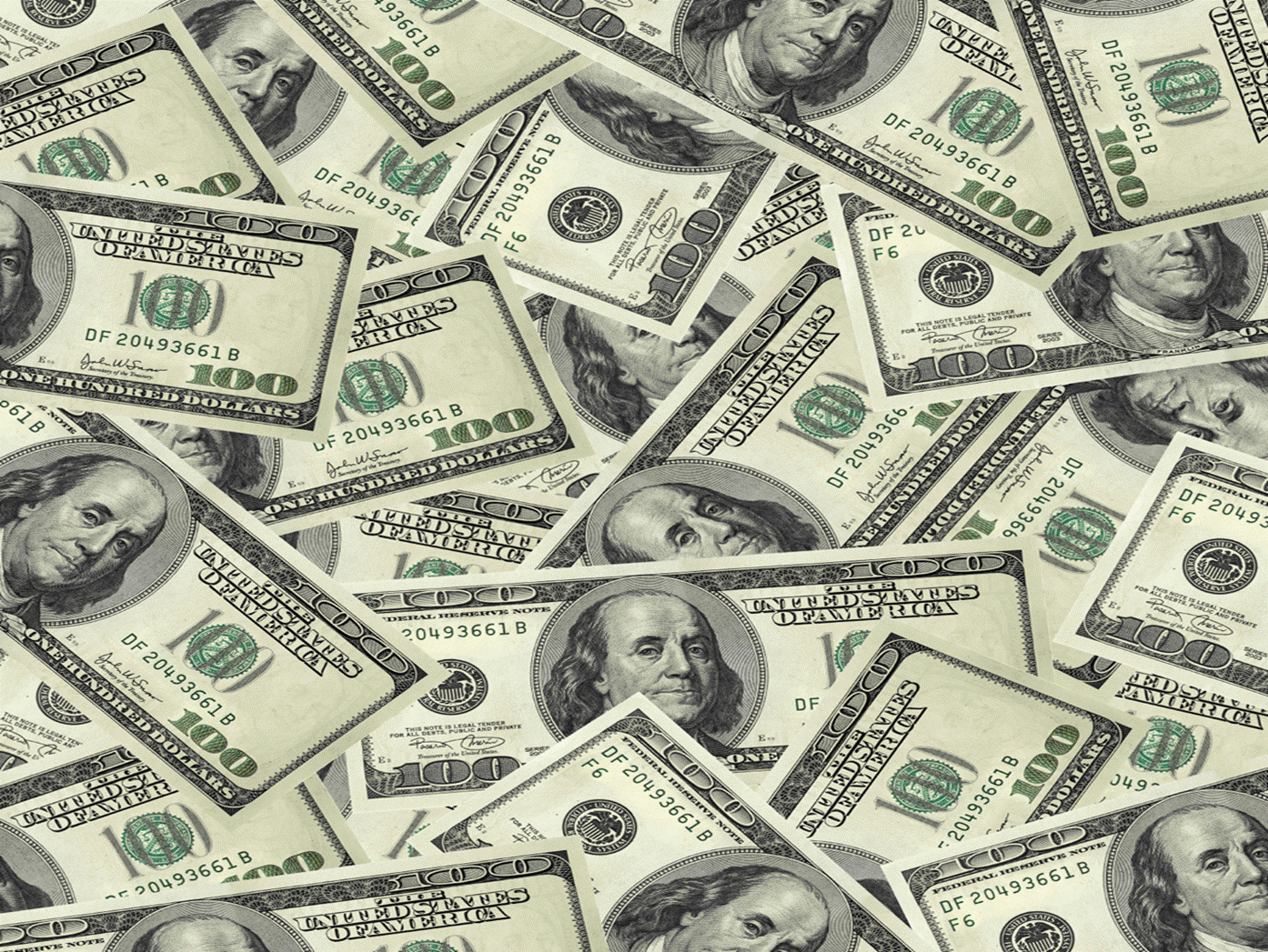
Reports​
- Bank Check Deposit Report
- Bank / Cash Voucher
- Payment Summary by Voucher No/ Date wise / Party Wise
- Receipt Voucher No/ Date wise / Party Wise